Q&A: #WRECares Partners with Julia Daviy to Donate Face Masks
Miami, FL – April 28, 2020 – #WRECares is proud to partner with Julia Daviy to donate face masks for front line workers. A fusion of artistic expression, digital design, and innovative science, inventor, environmentalist and designer Julia Daviy forges her aesthetic-driven DNA into all her bags and accessories; holding them to the highest ethical and environmental standards-while standing as true efficacies of exquisite taste.
In 2018, Julia Daviy presented the first ever collection of flexible and wearable clothes created digitally and printed out entirely on large-format industrial 3D printers; christening the concept of additive manufacturing—with a zero-waste production cycle and pioneering the practical use of 3D printing for achieving sustainability in the fashion products manufacturing. In the Spring of 2019, Julia Daviy launched the first digitally created and fully customizable 3D-printed skirts—named ‘must- haves’ by British Vogue. Later that year, Julia Daviy developed ‘soft geometry’ and multi-color 3D printing of flexible materials; yielding 4D and 3D printed suites. The examples of clothes representing these two techniques are a part of the exhibition ‘Feminist Futurist’ at The Boston Center for the Arts. Most recently in 2020, Daviy debuted a luxury brand of bags which will earn their place in the hearts of the fashion community forever.
Read the full Q&A below!
WRE: How did you get connected with #WRECares?
JD: We are connected through the members if the sustainable design community of Miami. Some of our friends and connections have already donated masks through the partnership with you. We just could not stay aside from this important community movement.
WRE: How is your company helping to fight COVID-19?
JD: New Age Lab works at the intersection of digital design, additive manufacturing, and ecology. Mainly we develop technological solutions and products for the fashion industry. Design products for fashion are available under my name, “Julia Daviy.” Recently we won Gold at Edison Awards 2020. I consider COVID -19 as a design challenge, the design challenge where we need to create and deliver not just the right products, but right decisions and proper solutions. We need to redesign not only how businesses and the entire economy works, but also how we work as a community and as a society. Masks, details of ventilators, face shields, and much other stuff could be digitally designed and 3D-printed. Covid-19 is an excellent illustration of how the community empowered by 3D printing technology can quickly solve the tasks where conventional manufacturing needs a lot of time. But not all of these solutions are the best possible solutions. The first stage in design thinking is a problem-finding, and what we saw in many cases was more about jumping straight to problem-solving. I do not want to discourage anyone; we had to act fast to protect ourselves as a society, and in many cases, a fast decision is better than a right decision if the last one is delivered with a considerable delay. At the same time, that may mean spending a lot of time and effort in the wrong direction. We decided to focus on the problem research to be able to donate our efforts meaningfully. Speaking of masks, the main problem that conventional cotton and other woven fabrics are ineffective protection against viruses, and 3D-printed masks are not comfortable. Moreover, their 3D printing takes a lot of time. Our capacities are not large, as we mainly do research and product development, so we focused on developing safer masks and tried to deliver better solutions here.
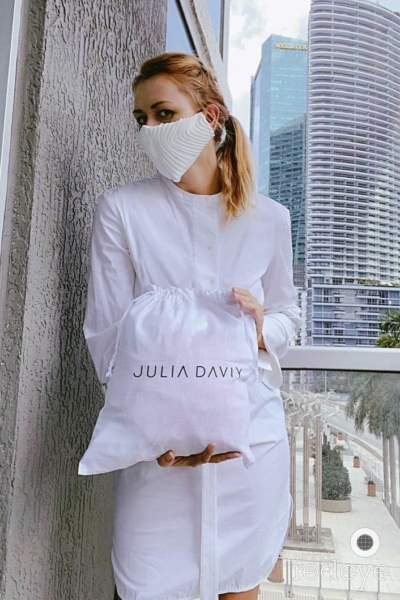
Julia Daviy
Covid-19 is an excellent illustration of how the community empowered by 3D printing technology can quickly solve the tasks where conventional manufacturing needs a lot of time.
Julia Daviy
WRE: Why did you want to get involved?
JD: For us, it was just a question whether we deliver our masks on our own or in partnership with a good organization. I am the kind of person who accepts challenges and goes to take part in the saving operations. And I love this activism on the community level. I think that what you guys do and what many makers and other active community members do today is just an excellent case of how communities could work effectively solving severe problems. Finally, we have dreamt about the active community here in Miami, and now we together take part in its building. Today many people are scared of uncertainty, and moral support is equally important as support with food or even money. We were lucky to finish our social project with 3D printing of the largest American flag and the first-ever 3D-printed flag that looks like fabric-made and can wave. Recently we got official confirmation, that we established the World Guinness Record. So we decided to dedicate this flag and the record to the resilience and perseverance of the American people, and honoring the victims, medical professionals, and communities impacted by COVID-19. ( Video: https://youtu.be/TCIdM4XO0Iw) What revolutionizes this flag, apart from its size, is a first of its kind process, making it soft enough to replicate a fabric flag waving in the wind.
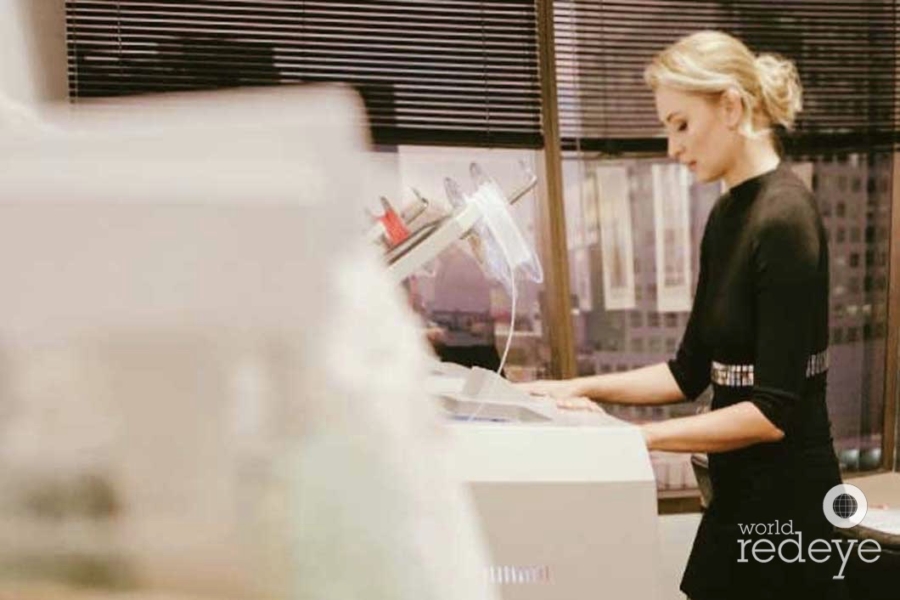
Julia Daviy
WRE: How were you able to involve your industry in the making of masks?
JD: Conventionally making cloth masks is a labor-intense process. And it’s very pity if these masks give a little or no protection. At the same time, if we modify the mask design and use 3D printing on fabrics (the direction which we pioneer), it is possible to reduce the labor involved in the mask production significantly. Unfortunately, 3D printing is not super fast yet, but anyway, it looks like a more meaningful solution comparing to cotton and other woven mask solution, as it also permits us to regulate the thickness and flexibility in different parts of the mask. Thanks to our solution with 3D printing on fabric, the nose and mouth areas of the masks are isolated, and a small filtration system is incorporated, at the same time, all the masks remain soft and comfortable. We imagined this collaboration as a design challenge to create protective masks and an opportunity to experiment and deliver different solutions. We created more than 20 prototypes, using different 3D designs and 3D printing technics and some of the best protective materials in the market.
WRE: What resources are needed to help increase your production of masks?
JD: As we see the technological way as a priority for the mask manufacturing, that means increasing in the number of large-format 3D printers.