Q&A: #WRECares Partners with Designer Patti Bruno of Josie Bruno Vintage – Vintage Camo with a New Purpose
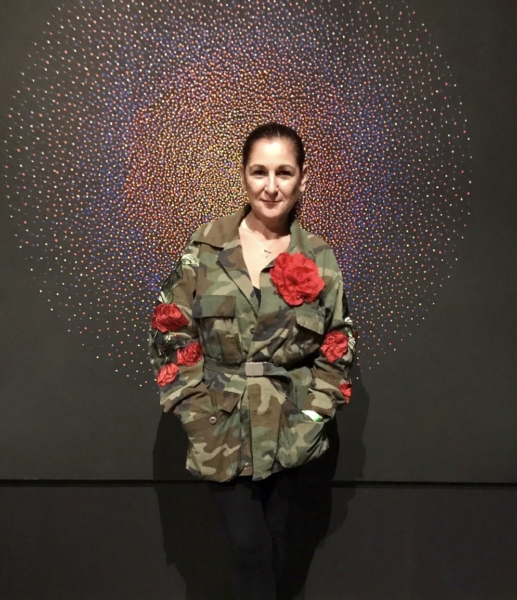
Patti Bruno
Miami, FL – April 3, 2020 –#WRECares has partnered with Miami-based designer and seamstress, Patti Bruno of Josie Bruno Vintage, to fight COIVD-19 by creating and donating handmade face masks to hospitals and those working on the front lines.
Patti is known for her signature bespoke camouflage jackets as seen on Jennifer Lopez, Dwyane Wade, Michelle Obama, Usain Bolt, Tyson Beckford, and Rocky Barnes. Patti Bruno’s mother, Josie Bruno, was a seamstress and collector of vintage jewelry and accessories. At an early age her mother taught her how to sew and the passion for cutting and sewing fabric remnants began. Patti remembers spending every Saturday in fabric mills searching for fabrics, trims and the perfect button for one of her Mom’s creations.
After 25 years in and around the retail industry, in 2014 she left her job and turned her sewing hobby into Josie Bruno Vintage. The DNA of her collection is vintage and always “camouflage”. While her styles are fashion forward they’re also sustainable. Patti’s zero-waste styles include a mix of vintage and new fabrics to create a truly one of a kind garment. All excess jacket parts are recycled to create linings, trims and hand sewn finishings. Today, Patti’s donating all recycled fabrics to provide masks for the Miami community. Each JBV jacket allows her to produce and donate four face masks.
Read the full Q&A below to see how Patti Bruno is helping fight the spread of COVID-19.
WRE: How did you get connected with #WRECares?
Patti Bruno: I was producing masks for Mask 4 Medicine and several friends connected me to Seth Browarnik.
WRE: How is your company Josie Bruno Vintage helping to fight COVID-19?
PB: I am donating 100% of mask production, material and labor.
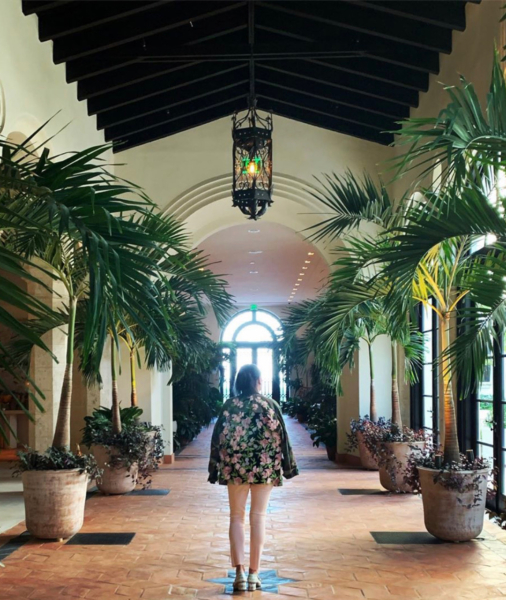
Patti Bruno
My company’s mission is to recycle and use every inch of the garment- this is a perfect project for me.
Patti Bruno
WRE: Why did you want to get involved?
PB: My company produces one of a kind vintage camo jackets. The process is to cut the back out of each jacket and insert a new one. I have accumulated over 1,000 jacket backs from jackets sold. As my pop-up shop and all of my retail partners closed their shops, I put my jacket production on hold and transitioned into mask making. I work from home and I was sitting here with over a thousand pieces of fabric and I began sewing. This is what I do for a living and it was natural. My company’s mission is to recycle and use every inch of the garment- this is a perfect project for me.
WRE: How were you able to involve your industry in the making of masks?
PB: I sell my jackets to 20 specialty stores and have dozens of clients who have purchased my jackets. They have gathered around via IG and have donated ribbons. For every jacket that I have sold = 4-6 masks have been made with the back of the jacket. My pop up shop in Wynwood has sold enough jackets to produce over 450 jackets. (The Shop in Pop Up Shop)
WRE: What resources do you need to help increase your production of masks?
PB: I am sewing every single mask, and have already made nearly 400 plus masks. Based on demand, I need assistance in sewing. I have the fabric and ribbon.